Was sind Reverse- und Generische-FMEAs?
Die „Reverse-FMEA“ findet man unter anderem in den CSR (Customer Specific Requirements) der PSA-Gruppe sowie bei GM. Dabei ist es keine neue FMEA-Art. Vielmehr geht es um den Zeitpunkt und die Vorgehensweise, wann und wie die FMEA reviewt und aktualisiert werden soll. Als präventive Methode startet die FMEA üblicherweise bereits sehr früh im Rahmen der Produkt- und Prozessentwicklung und findet ihren vorläufigen Abschluss mit dem Serienstart. Bei der „Reverse-FMEA“ wird nun das Lean Prinzip vom „Gemba“ aufgegriffen, bei dem direkt vor Ort durch Beobachten (Go and See) Probleme erkannt werden sollen. Dies kann natürlich erst spät im Entwicklungsprozess erfolgen, da z.B. für Prozess-FMEAs die Serienfertigung schon installiert und angelaufen sein muss.
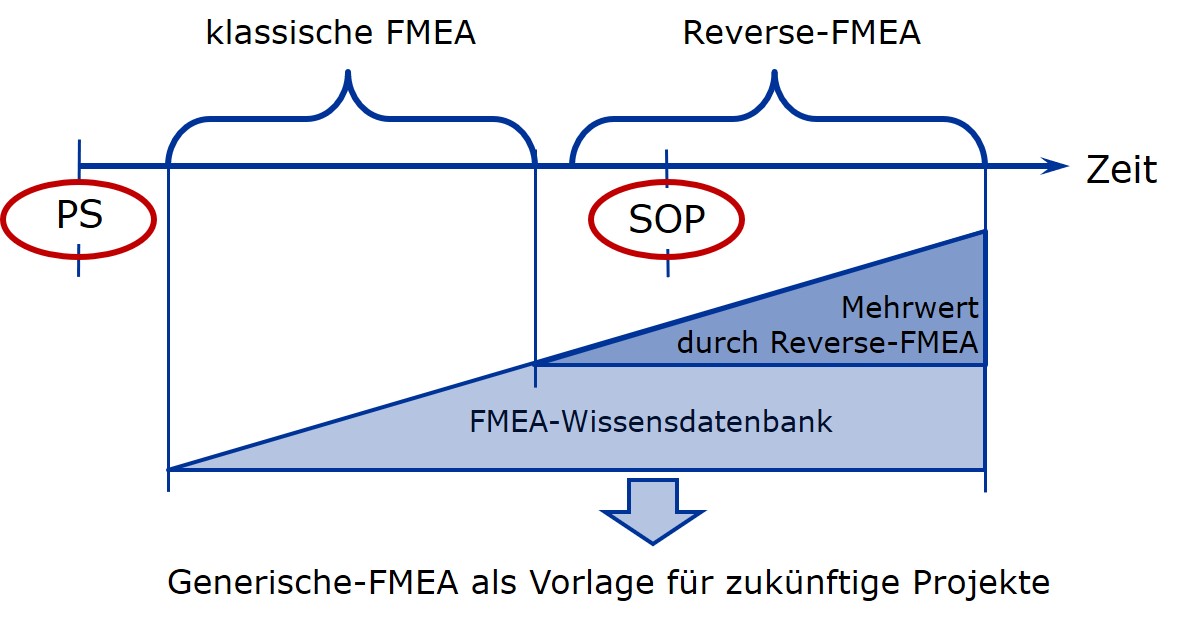
Obwohl dies dem präventiven Anspruch der FMEA etwas widerspricht, werden die bei der Beobachtung erkannten Probleme in die FMEA aufgenommen. Ziel dieser Vorgehensweise ist der Aufbau einer Wissensdatenbank. Wenn diese FMEA nun so gestaltet wird, dass sie als Vorlage für zukünftige Projekte genutzt werden kann, hat man eine „Generische-FMEA“ geschaffen. Damit wird eine effiziente und effektive Abwicklung von FMEAs ermöglicht und der gewünschte Mehrwert sollte sich bald einstellen. Anfangs wird man wohl zum Aufbau einer nutzbaren Wissensdatenbank etwas mehr Zeit investieren müssen, diese zahlt sich aber mit Sicherheit aus.
Was steckt hinter DRBFM?
Die „DRBFM-Methode“ (Design Review Based on Failure Mode) wurde Ende der 90er Jahre von Toyota aus der FMEA abgeleitet. Die Ziele von Toyota waren dabei unter anderem, die FMEA in das Design-Review zu integrieren und die Diskussion zu fördern. Nach einem anfänglichen Hype um diese neue Methode, ist diese aber rasch wieder abgeflaut. Ein Grund dafür war anscheinend, dass die klassische FMEA nach wie vor gefordert und DRBFM als Alternative nicht anerkannt wurde. Somit musste DRBFM immer zusätzlich zur FMEA durchgeführt werden. Dieser zusätzliche Aufwand war aber für die Meisten zu viel. Trotzdem ist die DRBFM-Methode, speziell in Branchen wo die klassische FMEA nicht zwingen gefordert wird (z.B. im Maschinenbau), eine überlegenswerte Alternative.
Wodurch unterscheidet sich aber die Methode DRBFM von der FMEA. Im Wesentlichen entfällt die 10 stufige Bewertung von B, A und E. Die identifizierten Risiken werden stattdessen nur in Themen mit hohem, mittlerem und niedrigem Risiko eingestuft. Außerdem ist die Analyse durch den Verantwortlichen soweit vorzubereiten, dass er seine Maßnahme zur Risikominimierung bereits auflistet. Diese Maßnahmen werden anschließend dem Steuerkreis vorgestellt. Die Experten diskutieren dann im Design-Review, ob diese Maßnahmen ausreichend sind oder noch zusätzliche Maßnahmen zur Risikominimierung oder besseren Risikoabschätzung getroffen werden müssen. Das DRBFM-Formblatt dazu gliedert sich somit in folgende zwei Bereiche (siehe Abbildung):
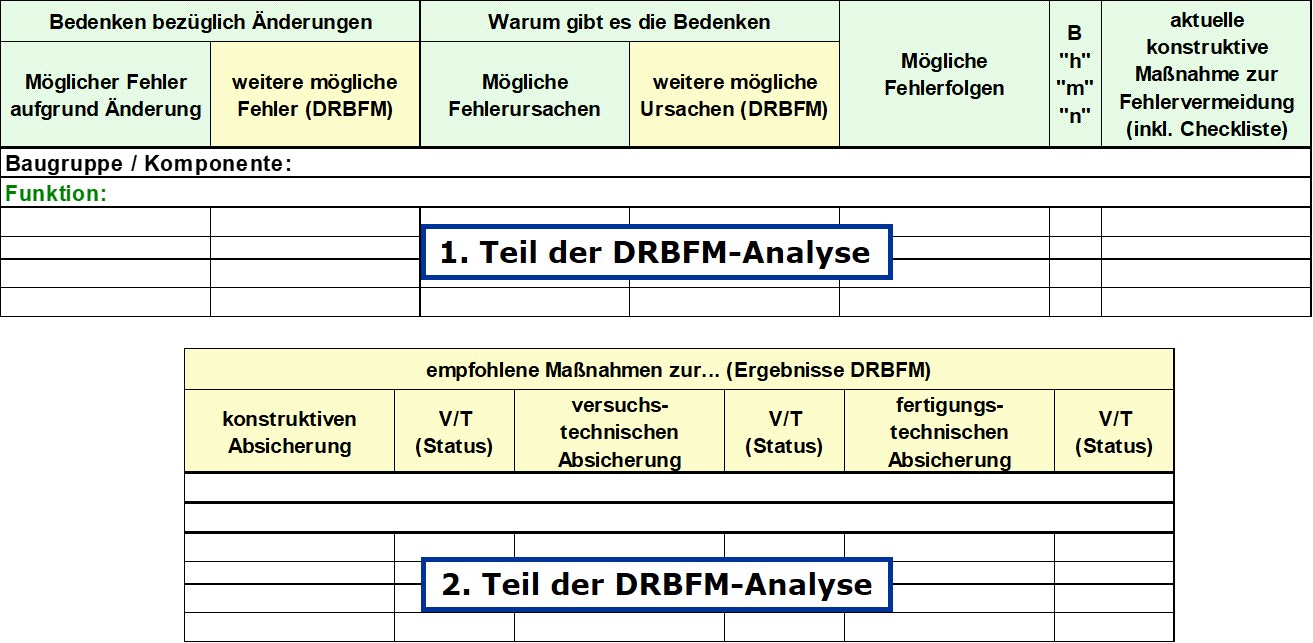
Wie werden Prüfschritte in einer Prozess-FMEA behandelt?
Vorzugsweise werden in einer Prozess-FMEA wertschöpfende Prozessschritte, die einen Mehrwert generieren, untersucht. Wenn jedoch eine eigene Prüfstation (z.B. EOL-Test, Dichtheitsprüfung) maßgeblich für die Beurteilung der Qualität eines Produktes ist oder erhebliche Investitionen damit verbunden sind, macht es durchaus Sinn, diese ebenfalls auf potentielle Risiken zu analysieren. Die Güte der dabei erzielten Messergebnisse stehen dabei im Fokus der Risikobetrachtung.
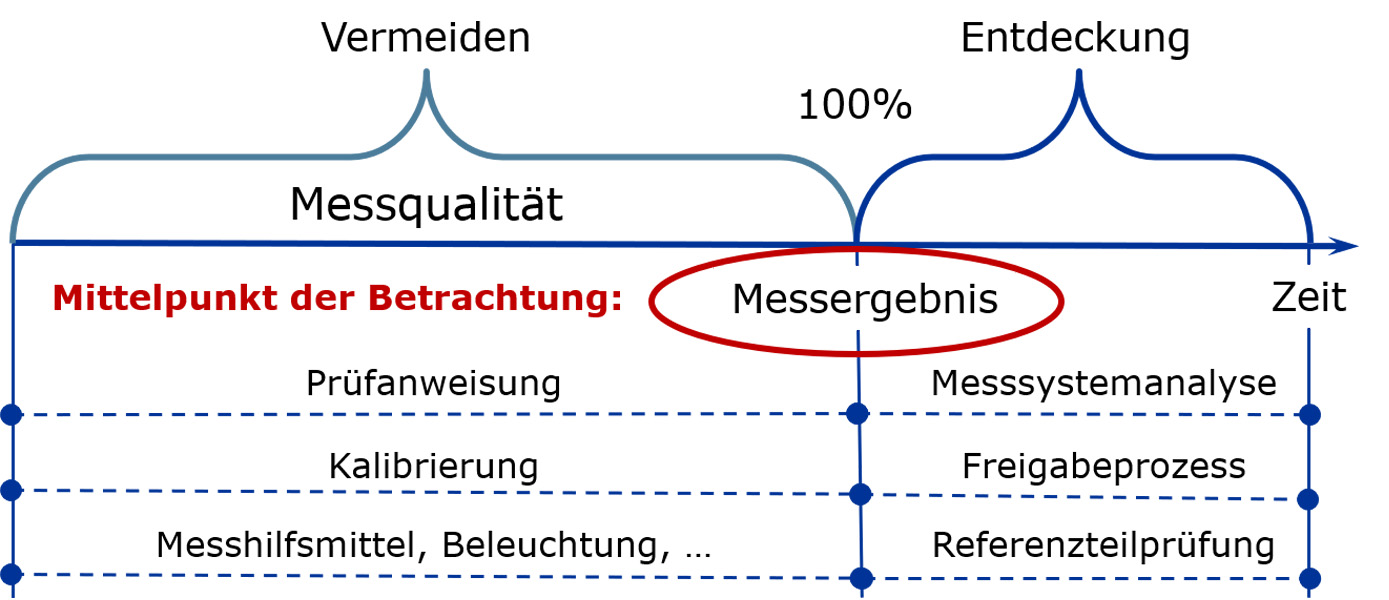
Daneben können auch
- die Beschädigung von den Produkten,
- die Beschädigung der Prüfstation selbst als auch
- die Verfügbarkeit der Prüfstation spannende Themen für eine FMEA-Betrachtung geben.
Ist eine Software-FMEA sinnvoll und welche Risken sollen analysiert werden?
Ja, so wie mechanische Systeme lässt sich auch eine Software sinnvoll mittels FMEA analysieren. Dabei ist es aber wichtig, für die Analyse die richtige Flughöhe zu definieren. Diese liegt auf Höhe der Produktintegration und Systemabnahme, nicht jedoch im Bereich der eigentlichen Programmierung. Einen anschaulichen Überblick des Aufbaus einer Software-FMEA zeigt nachfolgendes Ursache-Wirkungs-Diagramm, welches auch als Ishikawa-Diagramm bezeichnet wird.
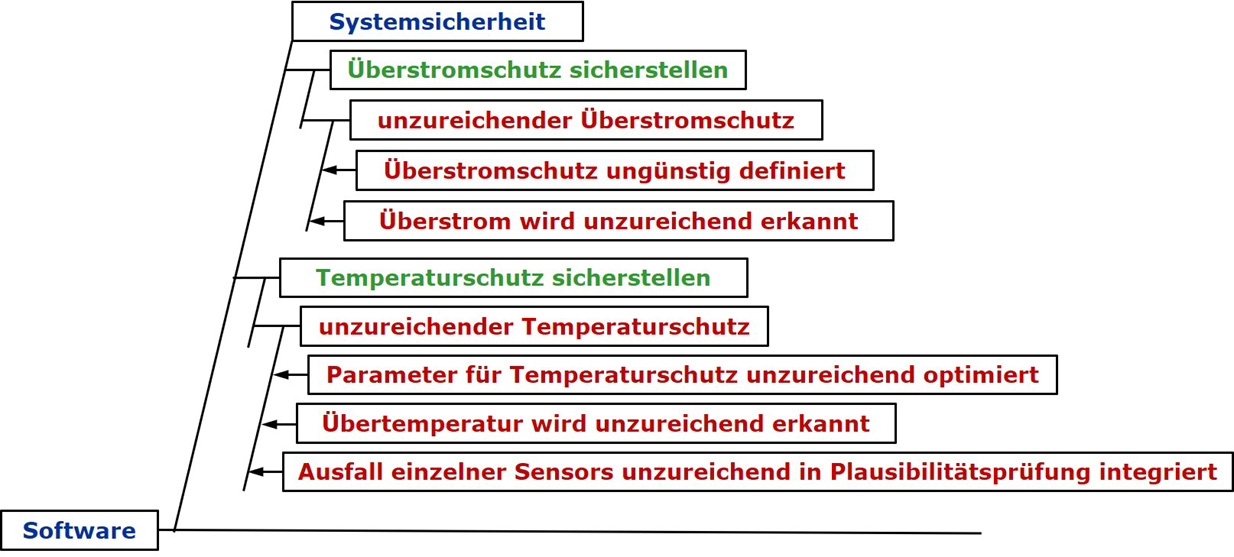
Dabei wird zuerst die Software im Rahmen der Strukturanalyse in kompakte Blöcke aufgesplittet (z.B. Systemsicherheit). Anschließend werden diesen Blöcken die Anforderungen zugeordnet. Welche Ergebnisse bzw. Resultate (z.B. Temperaturschutz sicherstellen) von der Software erwartet werden, stehen dabei im Mittelpunkt der Fragen. Werden diese Anforderungen negiert, so ergeben sich daraus die möglichen Fehler (z.B. unzureichender Temperaturschutz). Typische Ursachen, die zum Fehler führen, können sodann ungünstige Plausibilitätsprüfungen, unzureichend optimierte Parameter oder aber auch eine unzureichende Fehlererkennung sein.
FMEA online moderieren – ist dies effektiv möglich?
Ja es funktioniert und auch die dabei erzielten Ergebnisse, speziell die im Rahmen eine FMEA ausgearbeiteten und wichtigen Optimierungspotentiale, unterscheiden sich kaum von einer Präsenzmoderationen. Was sind aber die Voraussetzungen für eine erfolgreich Onlinemoderation?
Vor dem Corona-Lockdown haben wir uns nur am Rande mit den Tools für Videokonferenzen auseinandergesetzt. Wenn länderübergreifende Videokonferenzen notwendig waren, so fanden diese meist beim Kunden vor Ort statt und wir mussten uns nicht um technische Details kümmern. Mittlerweile sind aber viele der gängigen Softwaretools wie Microsoft-Teams, Zoom oder WebEx auf unseren Rechnern installiert. Dabei hat sich gezeigt, dass die Moderation mit all diese Softwareprodukten gut funktioniert Die gewählte Software ist nicht ausschlaggebend für den FMEA-Erfolg.
Vielmehr kommt es, wie auch bei der klassischen FMEA-Moderation, auf folgende Punkte an:
- Die richtige Vorbereitung und zeitliche Eintaktung: Neben einer kurzen FMEA-Schulung für das Team ist auch ausschlaggebend, dass alle relevanten und benötigten Unterlagen für die FMEA vorhanden und an die Teilnehmer verteilt sind. Auch die richtige terminliche und zeitliche Einplanung der FMEA-Sitzungen hat sich hier als Erfolgsfaktor erwiesen. Sind doch Online-Meetings durchaus anstrengender als Präsenzveranstaltungen.
- Die strukturierte Vorgehenswiese entsprechend den 7 Schritten einer FMEA: Dieser schon seit Jahren bewährte systematische Ablauf (die 5 Kernschritte gibt es offiziell schon seit 1996, sie wurden nur um eine Vor- und Nachbereitung ergänzt) bei der Moderation einer FMEA unterstützt das Team und den Moderator dabei, nie den roten Faden zu verlieren und die richtigen Fragen stellen zu können.
- Dem richtigen Team und den Softskills des Moderators: Die interdisziplinäre Zusammensetzung des Teams bringt auch bei einer remote moderierten FMEA die gewünschte Diskussionsbreite. Diesen Diskussionen ist wohl aufgrund der Entfernung und des fehlenden Sichtkontaktes schwerer zu folgen, verdeutlicht aber einen der wichtigsten Softskills von Moderatoren; nämlich zuhören können und das Diskutierte auf den Punkt bringen.
In den vergangenen Monaten konnten wir Erfahrung mit online moderierten FMEAs zu unterschiedlichen Themen und in unterschiedlichen Branchen sammeln. Wir waren unter anderem bei der Produkt- und Prozessplanung ganzer Batteriesysteme dabei, analysierten die gesamte Produktion eines neuen Medizinproduktes und optimierten eine Rohrproduktion mit Hilfe einer Familien-FMEA.
Haben Sie Fragen bzw. möchten auch Sie von unserer Erfahrung profitieren? Wir freuen uns auf Ihre Kontaktaufnahme.
Was sind die Voraussetzungen für eine erfolgreiche FMEA-Implementierung?
Eine erfolgreiche Implementierung der FMEA-Methode hängt im Wesentlichen vom Zusammenwirken der Faktoren Schulung, einer professionellen Anwendung sowie von der organisatorischen Verankerung der Methode ab.
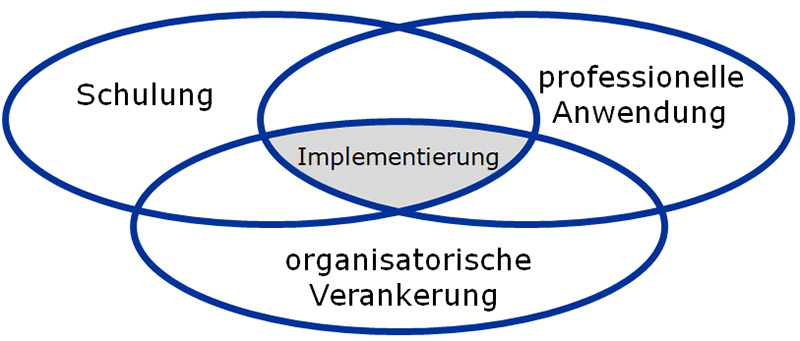
- Dabei ist im Rahmen der Schulung darauf zu achten, dass alle Teilnehmer durch ein Grundlagentraining mit der Vorgehensweise vertraut werden und ihre Rolle in den Workshops kennen. Darüber hinaus sind die Moderatoren in ergänzenden Methodenkenntnissen auszustatten.
- Nur Schulungen reichen jedoch in der Regel nicht aus. Die professionelle Anwendung der FMEA gerade in der Einführungsphase mittels ausgesuchter Pilotprojekte ist ebenso wichtig. Diese sollte durch erfahrene Moderatoren begleitet werden.
- Zu guter Letzt ist die Methode FMEA auch in der Auf- und Ablauforganisation entsprechend zu beschreiben. Dazu zählt neben einer Prozessbeschreibung auch die fixe Verankerung in den Projekten. Auch sind die notwendigen Formulare und Bewertungskataloge als Vorlagen (Templates) vorzubereiten.